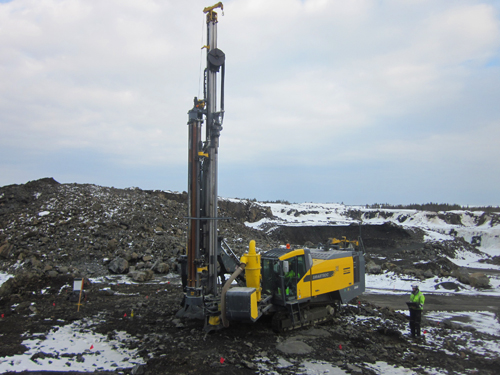
IMA stands for Innovative Mineral Analyzers and here is a company that does exactly what its name says. IMA is a technology front-runner in mining on-line analysis, and if that sounds dry, for mining companies concerned to occupy the critical space between metal prices and extraction costs material analysis can well be what decides viability. You can't plan based on what you don't know and IMA gives you the critical information often missing in mining; the value of the ore.
The company was formerly a part of the Finnish listed engineering group Outokumpu. In the 1990s, faced with a difficult global market, the group restructured around its core business spinning off IMA Engineering, which next January will be celebrating its 20-year anniversary as a private company whose shares are owned by a group of individuals and investors, including its Managing Director Mr Jukka Raatikainen. Jukka was already an experienced engineer and product manager at Outokumpu, and keen to develop products and technologies he had been working on that were then under development and bring them to market.
At the time of its foundation IMA was focused on concentrator applications, he says. “We were making analysers for measuring concentrator slurries. We were not involved in the core business of Outokumpu which was mainly to do with analysers for base metal mines. We were developing applications in other areas.” These included the X-ray Fluorescence (XRF) QuarCon system, an on-belt analyser system for monitoring crushed ore products, mainly in limestone and 'white minerals', and a sampling and analysis product for the cement industry called IMACON. Setting a pattern for its future business model IMA was already working with FLSmidth, the world-leading supplier of cement plants. The QuarCon and IMACON systems are still available, though technology never stands still and these products, leading edge at the time, are now classed as the firm's 'traditional' ranges, he says.
By 2000 IMA was already looking at ways to add value in the mining environment. “The in-house technical applications we had, Laser Induced Fluorescence (LIF) for example, led to products developed for the mines. For online measurement the big hurdle is sampling: we developed sampling methods and ways of adapting them from laboratory methods to online applications.” In a laboratory, he explains, samples are prepared, finely ground and examined in vacuum conditions. You may get a more accurate result with it on a spot sample than is possible when examining a fast-moving slurry or powder with on line methods. However, a good degree of analysis accuracy and excellent continuous sampling representativeness can be achieved by an online analyser, giving a reading every 30 seconds. That's real-time information. “With laboratory testing you are always viewing the process in the rear-view mirror!” he points out.
Limestone and cement processes are more tractable than those encountered underground. “Within a mine it is extremely difficult to reach analysis that gives a picture of the area where you are loading and blasting. That is why we developed a X-ray and laser-based conveyor fast analysis applications. Concentrators are stable. They stay in the same place. In a mine the operation is always moving and the sampling and analysis equipment has to move with the equipment.” IMA's OreSpex systems are designed to scan in real time the run-of-mine (ROM) ore being conveyed in mines and quarries. This is more than just a matter of good housekeeping: mines have become used to factoring in 'waste rock dilution' of between five and 20 percent. If too much waste material is getting into the feed the concentrator is running at lowered efficiency and that goes straight to the bottom line. “We believe it is very important to analyse the material at the point it goes on the conveyor. We offer the technology to analyse it within tenths of seconds, straight from the crusher – then if anything is wrong remedial action, like sorting out the unwanted waste rock or adjusting recovery process parameters according to ore characteristics before it enters the the plant, can be taken straight away.”
However waiting till the ore is blasted is too late to really avoid dilution problems. How is it possible to be sure you are only blasting and loading the ore and not waste rock ? To map the deposit geologists use drilling results of course, but this can be a slow process. Seven years ago IMA Engineering came up with its first on-site drill core analyser in cooperation with its sister company Mine On-Line Service. “In any typical exploration programme,” explains Jukka, “even on a greenfield site, you need to get samples of the ore body. During the exploration phase time is becoming very important. Investors want real time information. Quite often it can take ten years from starting drilling to getting a mine into operation. Even majors developing an established ore body don't want to take that long: for the juniors time is critical.” The company's response was to develop a scanning station in which cores could be analysed almost instantly and the analysis information could be delivered to mine planning programs within days or weeks instead of years as is the case with conventional technology.
The familiar pattern of exploring an area, whether in the mine or outside, is to box up the cores, log them and send them to the laboratory to be analysed. It can take six months to get the results back. “If you are in a drilling campaign you have to wait till you have those results before you can move on to plan the next holes to drill. We developed a machine that can analyse these drill cores immediately as they are put in the boxes, he says. “It is a factory-like process, in which these boxes are put in the scanning station and automatically analysed on the spot.” A scanning station of this type can handle up to 500 metres of drill core in a day: a drilling campaign of ten kilometres can thus be analysed within a month.
Mine ON-Line Service has been trialling and operating this service, known as Scanmobile, in the Nordic countries of Sweden, Norway and Finland since 2008 – with the emphasis on service. “The mining company doesn't have to buy the equipment – they just pay by the metre!” The equipment is installed in the Scanmobile van and moved from site to site, for the duration of the drilling campaign, he adds. “The information flows automatically from the van and the geologists can see it instantly via the internet. On the same day, or within a couple of days at most, they can download very accurate images of the drill cores, examine the boxes on-screen, and read the analysis.”
In practical terms, using Scanmobile gives the client the chance to move without delay to planning the next drill hole pattern and move on to the next drilling campaign. It is a very good example of IMA's focus on improving mine efficiency and getting the most out of the ore by addressing the real issues faced by mining companies.
Scanmobile service is delivered by Mine On-Line Service (MOLS), a kind of in-house partnership that works very well. However to take the products and services to a global market it is IMA's strategy to link up with larger equipment and systems companies where appropriate. Not all drills produce cores. It is also important to examine the material, known as drill cuttings, brought up by standard percussive or rotary drills – the information from the drill cuttings can't be as accurate as from a core but by using techniques perfected by IMA it can approach these levels. “We have now developed a method to analyse and feed online the results of drill cuttings using equipment that is installed and integrated with the drill rig,” says Jukka Raatikainen.
The new product and service, branded OreAlyzer, will be brought to market in partnership with the equipment manufacturer Atlas Copco. The analyser will be manufactured by IMA, integrated on Atlas Copco rigs and marketed integrally with them. “We wanted the best possible partner because this is a product with huge global potential,” he continues. “In drill cuttings analysis the challenge is to sample the material that comes out of the hole.” OreAlyzer analyses the elemental content of the cuttings, giving an instant reading. As the drill progresses it can analyse the material within 30 centimetre accuracy giving 'analyse while drilling' information which is processed in the rig's on-board computer and transmitted to the mine in real time along with data about the location, depth, hardness and penetration rate. “This is the best information you can get prior to blasting. It allows you to create a 3D model telling the mine where to blast.”
OreAlyzer is nothing less than a mining revolution, he believes, giving operators a new tool to work more accurately, position their blasting correctly, identifying the cut-off line, avoiding waste material sent to the concentrator and improving health and safety too. It is now available on AtlasCopco's highly automated D65 Smart Rock machine. “We are sure that in ten years all mines will have this on board their drilling rigs,” says Jukka confidently. “At present they don't know how much ore they are losing in the waste stream. They only have average results. A new world opens when you have a 3D model of the bench.”
IMA On-Line Mine Vision is behind all these products, and others it has in development. Accurate extraction of an accurately identified ore body and stable feed to the concentrator are business critical goals for mining companies. IMA is a research based company, and will continue to look for partners to adopt and market its products – privately owned, well-funded and with excellent links to universities and research institutions in Finland. There are many more applications for its technology says Jukka: “We are always looking for new applications in the market.” Those attracting his interest currently include slag analysis and the optimisation of laterite ore bodies but whatever the mine's problem IMA engineering is happy to discuss it, develop a solution, and hopefully bring it to the market in the shape of a product that will benefit the industry as a whole.
Written by John O'Hanlon, research by Marcus Lewis
DOWNLOAD
IMA-Euro-Mining-Aug13-Bro-s.pdf